Check Out the Globe of Light Weight Aluminum Spreading: Expert Keys and Approaches
In the world of manufacturing, light weight aluminum spreading stands as a crucial process, vital for the production of a vast range of items. Behind the relatively simple strategy lie a wide range of intricate facets, frequently unbeknownst to many. As we navigate via the world of light weight aluminum casting, there exists a realm of insider secrets and strategies that can raise the high quality of the end products and simplify the production procedure. By uncovering these concealed treasures and exploring the nuances of this craft, an entire brand-new dimension of possibilities emerges, assuring to revolutionize the means we view and engage with aluminum spreading.
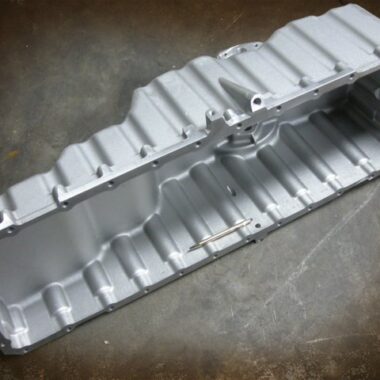
The Fundamentals of Aluminum Spreading
Light weight aluminum casting, a basic procedure in manufacturing, involves the pouring of molten aluminum right into a mold and mildew to achieve preferred forms and structures. This flexible method is widely used across different markets as a result of aluminum's exceptional homes such as high strength-to-weight ratio, corrosion resistance, and thermal conductivity.
The process starts with the melting of light weight aluminum in a heating system at temperature levels exceeding 1220 ° F(660 ° C ) When the light weight aluminum reaches its fluid state, it is poured right into a pre-designed mold tooth cavity. The mold, generally made from products like steel or sand, establishes the last shape of the actors light weight aluminum component.
After putting, the light weight aluminum is delegated cool and strengthen within the mold and mildew - about aluminum casting. This cooling period is critical as it determines the stability and top quality of the end product. Once strengthened, the mold is removed, exposing the newly developed aluminum spreading
Insider Tips for Effective Casting
To achieve ideal results in light weight aluminum spreading, precise attention to detail throughout the mold design phase is imperative for making certain effective results. Tracking and managing the steel temperature throughout the casting procedure can help avoid concerns such as premature solidification or porosity in the final item.
A well-prepared mold surface area can contribute to much better steel circulation, reduced turbulence, and boosted surface finish on the actors part. By paying close focus to these expert tips, producers can boost the quality and effectiveness of their light weight aluminum casting processes.
Advanced Strategies in Light Weight Aluminum Spreading
Using innovative methods and sophisticated methods, the world of light weight aluminum casting has seen a substantial development towards advanced methods that push the limits of conventional methods. One such technique is vacuum cleaner spreading, which involves producing a vacuum environment to get rid of air from the mold tooth cavity, resulting in greater high quality and even more intricate castings with decreased porosity. Additionally, investment casting, also understood as lost-wax spreading, is a polished method that enables intricate shapes and slim wall surfaces, resulting in exact and detailed read this article light weight aluminum parts.
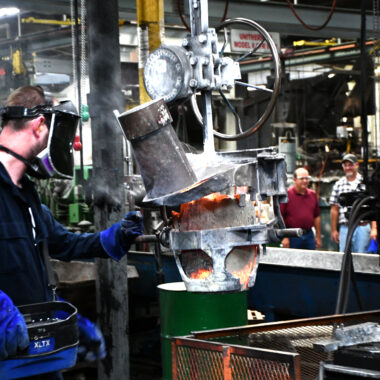
In addition, advanced simulation software program plays a crucial function in optimizing casting styles and anticipating prospective issues, permitting adjustments to be made before the real spreading process begins. By accepting these innovative strategies, producers can boost their aluminum casting capabilities to brand-new heights, meeting the demands of contemporary markets with precision and innovation.
Recognizing Different Casting Techniques
Different spreading methods offer one-of-a-kind benefits and are picked based on variables such as the intricacy of the style, production volume, product needs, and price considerations. One of the most usual casting methods is sand casting, where a mold is developed making use of sand as the key material.
Another preferred casting technique is pass away spreading, which involves infusing liquified steel right into a mold and mildew dental caries under high stress. Pass away casting is known for its high accuracy, smooth surface area coating, and the ability to generate intricate forms with tight resistances. Gravity spreading, on the other hand, counts on gravity to load the mold cavity with molten metal. This method appropriates for creating easier shapes and is economical for little to medium manufacturing runs. By understanding the subtleties of various casting approaches, producers can make enlightened decisions to optimize their production procedures and accomplish the desired outcomes.
Making Best Use Of Efficiency in Casting Workflow
With a strong grasp of the subtleties of different casting techniques, manufacturers can enhance their procedures to enhance efficiency in steel construction procedures. Making the most of performance in casting procedures calls for a systematic technique that focuses on enhancing every action of the casting process. One key approach is to implement lean production concepts to eliminate waste and boost overall efficiency. By determining and eliminating bottlenecks in the assembly line, my blog makers can boost workflow and lower lead times.
Moreover, buying advanced technology and equipment can dramatically enhance effectiveness in casting procedures. Automated systems, robotics, and computer-aided design (CAD) software application can enhance procedures, minimize errors, and rise result. In addition, training employees on the current techniques and best practices can also contribute to making the most of efficiency in casting procedures.
Regular maintenance of equipment and devices is vital to avoid break downs and reduce downtime - about aluminum casting. Applying a positive maintenance schedule can aid determine possible concerns prior to they rise, making certain smooth operations and continuous manufacturing. Generally, by prioritizing effectiveness and continual improvement, suppliers can maximize their casting procedures and remain competitive in the industry

Verdict
In conclusion, the globe of aluminum casting uses a large range of possibilities for those looking to create resilient and detailed steel objects. Recognizing the various casting methods and maximizing performance in procedures are crucial components to achieving high-quality outcomes in light weight aluminum casting.
One such strategy is vacuum spreading, which entails producing a vacuum cleaner environment to get rid of air from the mold and mildew cavity, leading to higher high quality and even more elaborate castings with lowered porosity (about aluminum casting). In addition, investment spreading, also known as lost-wax spreading, is a refined technique that permits for slim walls and intricate forms, resulting in specific and detailed aluminum parts
One of the most common casting methods is sand casting, where a mold and mildew is produced utilizing sand as the key product.An additional prominent casting approach is pass away casting, which includes infusing liquified metal right into a mold and mildew tooth cavity under high pressure. Comprehending the numerous casting techniques and maximizing performance in procedures are vital parts to attaining top notch results in aluminum spreading.